-
Alumina Ceramic Components
-
Ceramic Housing
-
Metallized Alumina Ceramics
-
Custom Ceramic Parts
-
Alumina Ceramic Insulator
-
Alumina Ceramic Rings
-
Pressure Sensor Ceramic
-
Advanced Technical Ceramics
-
Advanced Engineering Ceramics
-
Fuse Ceramic
-
Ceramic Connector Blocks
-
Electronic Ceramic Components
-
Magnetron Ceramic
-
Zirconia Ceramic Parts
-
Alumina Ceramic Rods
-
Mr.FarnReply very fast and easy to talk!
-
Mr.JacksonGood service and nice to talk.
95% Fine Alumina Ceramic O Ring
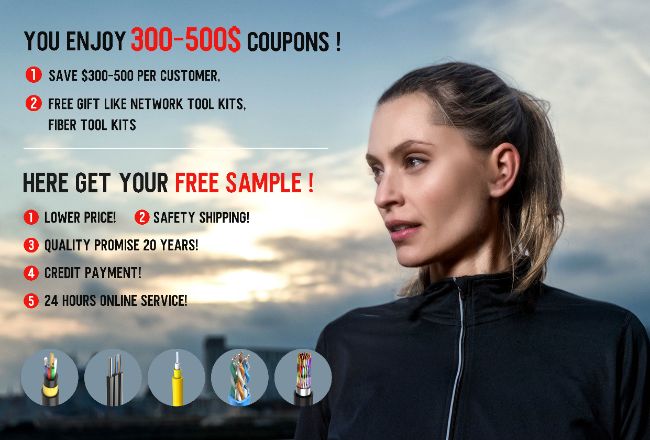
Contact me for free samples and coupons.
Whatsapp:0086 18588475571
Wechat: 0086 18588475571
Skype: sales10@aixton.com
If you have any concern, we provide 24-hour online help.
xProduct Name | Metallized Alumina Ceramic Rings / Ceramic Insulators For Battery | Material | Alumina (Aluminum Oxide, Al2O3) |
---|---|---|---|
Insulation Resistance | 1000M Ω(1000VDC) | Thermal Shock Resistance Room Temperature To 850C | Will Not Burst Or Leak After Five Operations |
Max. Use Temp. | 1650℃ | Water Absorption | 0 |
ROHS Hardness | ≥89 | Flexural Strength | 550 Mpa(psix10^3) |
Compressive Strength | 2600(377) Mpa(psix10^3) | Coefficient Of Thermal Expansion | 8.2 X10^-6/℃ |
Coefficient Of Thermal Conductivity | 17-30.4 W/m.K | ||
Highlight | Alumina Ceramic O Ring,ISO14001 Ceramic O Ring,ISO14001 alumina ceramic machining |
Alumina Seal Ceramic Rings / Industry Insulation Rings
1. Description:
The hardness of high-temperature structural ceramics is much higher than that of metals, and the wear resistance at high temperatures is better than that of metals, and especially better than cemented carbide. Metal and ceramic pair sliding. Under lubricated conditions, not only the wear of ceramics is extremely small, but the wear of metal is also smaller than when metals are paired. Most of the parts of the valve mechanism slide at high speed under high load and insufficient lubrication conditions. It is very suitable for ceramic manufacturing to reduce wear. The main disadvantage of ceramic parts in terms of performance is that they are prone to internal cracks during manufacturing. The internal cracks may propagate under stress and cause brittle failure of parts. In addition, temperature sudden changes caused by changes in engine operating conditions, surface damage caused by wear and foreign objects, etc., may affect the reliability and service life of the parts. By applying ceramic coating, the temperature in the combustion chamber of the engine can be improved, and the working efficiency of the engine can be improved.
2. Feature Advantages:
1) Refractory, High Temperature Resistance, Maximum Used Temperature: 1800 ºC (3272ºF)
2) Hardness Strength, Wear Resistance Up To Mohz 9.0 ; HRA 80-90
3) High Voltage, Good Insulation Performance ,Electrical Resistivity Up To 10∧14 Ohm.Cm
4) High Polished Surface Up To Rz0.8(Ra0.1)
5) Superior Mechanical Strength, MAX 10 MPa.m1/2 Fracture toughness
6) Pressure Resistance, Max 2300MPa compressive strength
7) Anti-High Corrosion Resistance, Such As Acid Alkali Resistance
8) Long Service Life
3. Material Features / Properties:
Color | White or Ivory | White or Ivory | White or Ivory | |
Density | g/cm 3 | 3.82 | 3.9 | 3.92 |
Hardness | HRA | 83 | 85 | 85 |
Flexural Strength | Mpa (psi*10 3 ) | 375 | 386 | 381 |
4. Technical Parameters:
Technical Parameters of Ceramics | ||||||||
Items | Test Conditions | Unit or Symbol | 99% AL2O3 | 95% AL2O3 | 90% AL2O3 | Zirconia | Steatite | Silicon Carbide |
Volume Density | -- | g/cm3 | ≥3.70 | ≥3.62 | ≥3.40 | ≥5.90 | ≥2.60 | ≥3.08 |
Tightness | -- | Pa·m³/s | ≤1.0×10-11 | ≤1.0×10-11 | ≤1.0×10-11 | - | - | - |
Liquid Permeability | -- | -- | Pass | Pass | Pass | Pass | - | |
Flexural Strength | - | MPa | ≥300 | ≥280 | ≥230 | ≥1100 | ≥120 | ≥400 |
Elastic Modulus | - | GPa | - | ≥280 | ≥250 | ≥220 | - | 400 |
Poisson Ratio | - | - | - | 0.20~0.25 | 0.20~0.25 | - | - | - |
Thermal Shock Resistance | 800℃( Room Temperature) Cycle: 10 times | Pass | Pass | Pass | - | - | - | |
Coefficient of Linear Expansion | 20℃~100℃ | ×10-6 K-1 | - | - | - | ≤8 | - | |
20℃~500℃ | ×10-6 K-1 | 6.5~7.5 | 6.5~7.5 | 6.5~7.5 | 6.5~11.2 | - | - | |
20℃~800℃ | ×10-6 K-1 | 6.5~8.0 | 6.5~8.0 | 6.3~7.3 | - | 4 | ||
20℃~1200℃ | ×10-6 K-1 | - | 7.0~8.5 | - | - | - | - | |
Coefficient of Thermal Conductivity | 20℃ | W/(m·k) | - | - | - | - | - | 90~110 |
1000℃ | ||||||||
Dielectric Constant | 1MHz 20℃ | - | 9.0~10.5 | 9.0~10 | 9.0~10 | - | ≤7.5 | - |
1MHz 50℃ | - | - | 9.0~10 | - | - | - | - | |
10GHz 20℃ | - | 9.0~10.5 | 9.0~10 | 9.0~10 | - | - | - | |
Volume Resistivity | 100℃ | Ω·cm | ≥1.0×1013 | ≥1.0×1013 | ≥1.0×1013 | - | ≥1.0×1012 | - |
300℃ | ≥1.0×1013 | ≥1.0×1010 | ≥1.0×1013 | - | - | - | ||
500℃ | ≥1.0×109 | ≥1.0×108 | -- | - | - | - | ||
Disruptive Strength | D.C | kV/mm | ≥17 | ≥15 | ≥15 | - | ≥20 | - |
Chemical Durability | 1:9HCl | mg/c㎡ | ≤0.7 | ≤7.0 | - | - | - | - |
10%NaOH | mg/c㎡ | ≤0.1 | ≤0.2 | - | -- | - | - | |
Grain Size | - | μm | - | 3~12 | - | - | - | - |
5. Process Flows:
Formulating --- Granulating --- Forming --- Sintering --- Grinding --- Printing --- Nickel Plating --- Assembing --- Brazing --- Inspecting --- Packing
6. Production Facilities: Prilling Tower , Forming Machine , High Temperature Sintering Kiln
7. Detection Devices:
Electric Performance Tester , Film Thickness Analyzer , Granulometer , Helium Mass Spectrometer Leak Detector , Universal Pull Force Meter
8. Our advantages: Quality Assurance ; Price Competitive ; Factory Supply Directly ; Good Service
9. Shipping and Package:
10. Our aimed market:
Notes:Above information only for reference and please contact with us for more details freely when you have any inquiry!