-
Alumina Ceramic Components
-
Ceramic Housing
-
Metallized Alumina Ceramics
-
Custom Ceramic Parts
-
Alumina Ceramic Insulator
-
Alumina Ceramic Rings
-
Pressure Sensor Ceramic
-
Advanced Technical Ceramics
-
Advanced Engineering Ceramics
-
Fuse Ceramic
-
Ceramic Connector Blocks
-
Electronic Ceramic Components
-
Magnetron Ceramic
-
Zirconia Ceramic Parts
-
Alumina Ceramic Rods
-
Mr.FarnReply very fast and easy to talk!
-
Mr.JacksonGood service and nice to talk.
95 Industrial Aluminum Oxide Ceramics Brazed Ceramic To Metal Impact Resistance
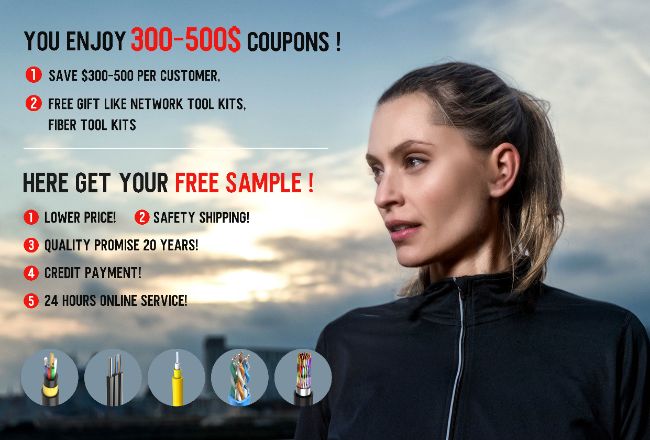
Contact me for free samples and coupons.
Whatsapp:0086 18588475571
Wechat: 0086 18588475571
Skype: sales10@aixton.com
If you have any concern, we provide 24-hour online help.
xChemical Ingredients | Al2O3 | Max. Use Temp. | 1650℃ |
---|---|---|---|
Bulk Density | 3.6g/cm3-3.9g/cm3 | Water Absorption | 0% |
ROHS Hardness | ≥85 | Flexural Strength | 358(52) - 550 Mpa(psix10^3) |
Compressive Strength | 2068(300) - 2600(377) Mpa(psix10^3) | Coefficient Of Thermal Expansion | 7.6 - 8.2 / 1X10^-6/℃ |
Coefficient Of Thermal Conductivity | 16-30.4 / W/m.K | Thermal Shock Resistance | 250℃ |
Dielectricity Constant | 9-9.7 / 1MHz.25℃ | Dielectric Strength | 8.3(210) - 8.7(220) / Ac-kV/mm(ac V/mil) |
Volume Resistivity | >10^13 Ohm-cm | ||
Highlight | 95 aluminum oxide ceramics,Impact resistance aluminum oxide ceramics,95 industrial ceramic components |
Alumina ceramic components / relay ceramic assemblies / ceramic - metal brazed contactor
1. Description:
The assessment of the measurement uncertainty is an indispensable task in all calibration procedures. By international accord, the evaluation is to be done in accordance with the ISO Guide to the Expression of Uncertainty in Measurement (GUM). To calibrate the positional deviations of computer numerically controlled (CNC) machine tools, calibration laboratories will usually follow the guidelines in ISO 230-2 International Standard. However, that standard does not address uncertainty. In this paper, we present an uncertainty evaluation scheme that is firmly grounded in the GUM, and can therefore be of use as a guide to develop appropriate uncertainty calculations in this and similar types of calibrations.
2. Feature Advantages:
1) High stability
2) High welding sealing performance
3) High hardness and high density
4) Low thermal conductivity
5) High temperature resistance
6) A variety of specifications is available
3. Material Features / Properties:
Color | White or Ivory | White or Ivory | White or Ivory | |
Density | g/cm 3 | 3.82 | 3.9 | 3.92 |
Hardness | HRA | 83 | 85 | 85 |
Flexural Strength | Mpa (psi*10 3 ) | 375 | 386 | 381 |
4. Technical Parameters:
Technical Parameters of Ceramics | ||||||||
Items | Test Conditions | Unit or Symbol | 99% AL2O3 | 95% AL2O3 | 90% AL2O3 | Zirconia | Steatite | Silicon Carbide |
Volume Density | -- | g/cm3 | ≥3.70 | ≥3.62 | ≥3.40 | ≥5.90 | ≥2.60 | ≥3.08 |
Tightness | -- | Pa·m³/s | ≤1.0×10-11 | ≤1.0×10-11 | ≤1.0×10-11 | - | - | - |
Liquid Permeability | -- | -- | Pass | Pass | Pass | Pass | - | |
Flexural Strength | - | MPa | ≥300 | ≥280 | ≥230 | ≥1100 | ≥120 | ≥400 |
Elastic Modulus | - | GPa | - | ≥280 | ≥250 | ≥220 | - | 400 |
Poisson Ratio | - | - | - | 0.20~0.25 | 0.20~0.25 | - | - | - |
Thermal Shock Resistance | 800℃( Room Temperature) Cycle: 10 times | Pass | Pass | Pass | - | - | - | |
Coefficient of Linear Expansion | 20℃~100℃ | ×10-6 K-1 | - | - | - | ≤8 | - | |
20℃~500℃ | ×10-6 K-1 | 6.5~7.5 | 6.5~7.5 | 6.5~7.5 | 6.5~11.2 | - | - | |
20℃~800℃ | ×10-6 K-1 | 6.5~8.0 | 6.5~8.0 | 6.3~7.3 | - | 4 | ||
20℃~1200℃ | ×10-6 K-1 | - | 7.0~8.5 | - | - | - | - | |
Coefficient of Thermal Conductivity | 20℃ | W/(m·k) | - | - | - | - | - | 90~110 |
1000℃ | ||||||||
Dielectric Constant | 1MHz 20℃ | - | 9.0~10.5 | 9.0~10 | 9.0~10 | - | ≤7.5 | - |
1MHz 50℃ | - | - | 9.0~10 | - | - | - | - | |
10GHz 20℃ | - | 9.0~10.5 | 9.0~10 | 9.0~10 | - | - | - | |
Volume Resistivity | 100℃ | Ω·cm | ≥1.0×1013 | ≥1.0×1013 | ≥1.0×1013 | - | ≥1.0×1012 | - |
300℃ | ≥1.0×1013 | ≥1.0×1010 | ≥1.0×1013 | - | - | - | ||
500℃ | ≥1.0×109 | ≥1.0×108 | -- | - | - | - | ||
Disruptive Strength | D.C | kV/mm | ≥17 | ≥15 | ≥15 | - | ≥20 | - |
Chemical Durability | 1:9HCl | mg/c㎡ | ≤0.7 | ≤7.0 | - | - | - | - |
10%NaOH | mg/c㎡ | ≤0.1 | ≤0.2 | - | -- | - | - | |
Grain Size | - | μm | - | 3~12 | - | - | - | - |
5. Process Flows:
Formulating --- Granulating --- Forming --- Sintering --- Grinding --- Inspecting --- Packing
6. Application Fields:
New energy vehicles, charging piles, solar power generation, energy storage and power storage system, electric vehicle power system and so on.
7. Production Facilities: Prilling Tower , Forming Machine , High Temperature Sintering Kiln
8. Detection Devices:
Electric Performance Tester , Film Thickness Analyzer , Granulometer , Helium Mass Spectrometer Leak Detector , Universal Pull Force Meter
9. Order Flow Steps as belows: Inquiry ---Quotation --- Place an order --- Production --- Delivery
10. Our advantages: Quality Assurance ; Price Competitive ; Factory Supply Directly ; Good Service
11. Shipping and Package:
12. Our aimed market:
13. Guiding questions for material selection:
In order to select the appropriate material for your application, there are several questions that you should consider.
1) Are the mechanical properties important?
2) Will the part be exposed to wear/friction/impacts?
3) How many pieces are you looking to have made in your first batch?
4) What type of atmosphere will the part be operating in; inert or oxidizing?
5) What is the maximum operating temperature of the component?
6) Will the component experience any thermal shock?
7) Is electrical insulation important?
8) Is thermal conductivity important?
9) How important are tolerances and surface finish?
Notes:Above information only for reference and please contact with us for more details freely when you have any inquiry!